by Steve Ragan, Director, Research and Technical Services
The answer to this controversial question, from both angles, is a qualified “yes.” Vapor barriers have been associated with certain concrete slab-on-grade problems including curling and cracking. But they have also proven to be beneficial in reducing failures of moisture-sensitive flooring materials, adhesives, and coatings caused by excessive emission of moisture vapor from concrete slabs. Therefore, it is understandable that designers and contractors on both sides of the question have justifiable arguments that cannot be easily dismissed.
Before one can make the best decision regarding whether or not to place a vapor barrier under a concrete floor slab-on-grade, it is important to understand the sources of moisture, how it moves through the slab, and how it adversely affects certain floor coverings, adhesives, and coatings.
The excess or free water within the concrete is the source of some of the moisture in a slab. Concrete requires sufficient water both to hydrate the cement in the mixture and to create a workable consistency. Cement hydration is simply the chemical reaction that occurs between water and cement, which causes the concrete to attain a set and to gain strength and durability. Water in excess of that needed for hydration (sometimes called water of convenience), is only required to make the concrete easier to place, consolidate, and finish. Once the concrete has been placed, finished, and cured, some of the excess water of convenience must escape in order for the slab to meet the manufacturer’s moisture emission requirements for the floor covering, adhesive, or coating. Many manufactures require that the moisture emission rate from concrete not exceed 3.0 pounds of water per 1000 square feet in 24 hours. This requirement is very challenging when one considers that a 4-in. thick slab, constructed with concrete having a 0.50 water-cement ratio (w/c) and a 4-in. slump, can contain between 1600 and 1700 pounds of free water in a 1000-square-foot area!
The rate that moisture escapes from a slab depends on the concrete w/c, the density of the finish, the ambient conditions above the slab, and the moisture below the slab. One laboratory drying study indicated that 4-in. thick concrete samples, having a w/c=0.50 and sealed from below, required 82 days for the vapor emission rate to reach 3.0 pounds per 1000 square feet per 24 hours. The ambient air above the sample was 73°F and 50% relative humidity. The same concrete not sealed from below required 144 days to reach the same vapor emission rate. Concrete having a w/c=0.40 and sealed from below required 46 days to reach the 3 pound per 1000 square feet per 24 hour vapor emission rate, while the same concrete not sealed from below required 52 days to achieve this rate. This study reinforces the benefit of using concrete having a w/c less than 0.50, and the need to reduce the slab moisture entering from below when moisture-sensitive flooring materials will be installed.
A natural source of water can be found at some depth below most building sites. This water can generally move upward through soil and contact the bottom of a slab-on-grade in one of two ways. The first way is through capillary action. Capillary action uses the forces of adhesion, surface tension, and cohesion to cause the water to be drawn upward above the water table through the very narrow passageways found in many soils. An example of capillary action is water rising to a higher elevation inside a narrow straw that is placed into a glass of water. Capillary action in soils can be interrupted by a capillary break, such as a layer of crushed stone between the slab and the subgrade.
Although a capillary break may stop the rise of water in a liquid state, it does not eliminate the potential for moisture vapor to reach the slab. Water changes from a liquid to a vapor as it evaporates, and water vapor will move from areas of high to low vapor pressure. This process of vapor movement is termed “diffusion” and occurs in both soil and concrete. Several investigations have shown that the relative humidity in the base and subgrade just beneath the slab is near 100%, regardless of the depth of the water table. Although capillary action can cause liquid water to rise, diffusion is how water vapor distributes itself above the water table. Unless this diffusion is restricted, water vapor will contact and enter the slab. In the absence of effective moisture protection directly beneath the slab, the high humidity environment beneath the slab can contribute to an increase in moisture within the concrete over time.
Moisture-induced failure of flooring materials may appear in the form of cupping, bulging, or swelling. Failure of floor coatings typically manifests as blistering. As moisture moves toward the top of a slab, soluble alkalies are frequently carried with it. This causes the pH level at the surface to increase above the 9 to 10 pH limit of most modern flooring adhesives, which in turn leads to a breakdown or re-emulsification of the adhesive. The use of a vapor barrier (more accurately termed a vapor retarder), having a water vapor permeance of less than 0.3 perm is frequently used to retard the flow of moisture through the slab. These vapor retarders are typically polyethylene or polyolefin sheeting materials. While the permeance of the vapor retarder is important, its ability to withstand construction activity is also important. A vapor retarder that is torn or punctured provides a pathway for moisture to enter the slab from below. The American Concrete Institute’s Guide for Concrete Floor and Slab Construction recommends that the thickness of the vapor retarder be at least 10 mils. Puncture studies of 6-, 8-, 10-, and 20-mil vapor retarder materials have shown that 10 mils is the minimum thickness that should be considered, and thicker material may be necessary over angular base materials.
Because the permeability of concrete increases with an increase in its w/c, a low w/c concrete mixture should be considered in floor slabs where moisture-induced failure of flooring materials is a concern. Watertight concrete is often considered to have a w/c less than 0.50. However, using a concrete with a low w/c alone is often insufficient to satisfy the floor covering industry’s moisture emission requirements. Even after what appears to be sufficient drying of the surface, moisture will redistribute itself once the floor is covered. Without sufficient subslab moisture protection the total moisture in the slab will increase over time, and sawed contraction joints and random cracks will provide passageways for moisture to migrate through the slab. Omitting a vapor retarder may also result in liability for a flooring failure, since its use is often published in guidelines from many flooring manufacturers.
Placement location of vapor retarders is often a source of confusion for designers and contractors. Until 2001, the American Concrete Institute (ACI) recommended 4″ of granular fill be placed atop vapor retarders. However the ACI has since revised this recommendation because of their recognition that fill courses above the vapor retarder may sometimes take on water from rainfall, curing, or sawcutting. As a result, the ACI Committee 302 now recommends that floor slabs-on-grade being covered with moisture-sensitive coverings have the vapor retarder placed on top of dry granular fill and directly beneath the slab.
Confusion and debate over the use of vapor retarders will likely continue into the future. However, the fact that the cost of floor coverings over concrete floor slabs in the U.S. is now estimated at over one billion dollars a year requires that greater attention be given to concerns about moisture within and below these slabs. Each project should be considered individually; however, the following general recommendations are useful in mitigating moisture-related problems in concrete floor slabs-on-grade:

Feel like taking to the ice? Skid the stones across the slippery surface, but don't push them too hard! Crack Hair Fix Styling Cream provides the thermal protection against blow-drying, flat & curling irons. Your hair can remain healthy while looking exactly how you want it to look. GOODBYE FRIZZY HAIR: Crack Hair Fix Styling Cream Formula is specially created to block the effects of humidity and eliminate up to 95% of frizz for up to 24 hours!
- Use a low permeance vapor retarder to protect floor slabs that will be covered with moisture-sensitive floor coverings, adhesives, and coatings. Floor covering manufacturer’s published literature should be consulted.
- Include a capillary break of granular material below the slab. However, recognize that the capillary break will not prevent moisture from reaching the slab in vapor form.
- Consider using concrete having a w/c not greater than 0.45 to hasten slab drying time. Use of fly ash may help reduce soluble alkali content in the slab.
- Place the vapor retarder on top of the granular material and directly beneath the slab for moisture-sensitive floor covering and coating applications. However, in doing so, recognize that additional attention should be given to the design of reinforcement so that potential curling stresses within the slab are addressed.
- Use a 15 mil or thicker vapor retarder material, particularly if it will be subjected to traffic from ready-mixed concrete trucks, concrete buggies, or laser screeds.
- Cover slabs for 7-days with sheet material rather than using membrane curing compounds in order to minimize drying time and surface preparation costs.
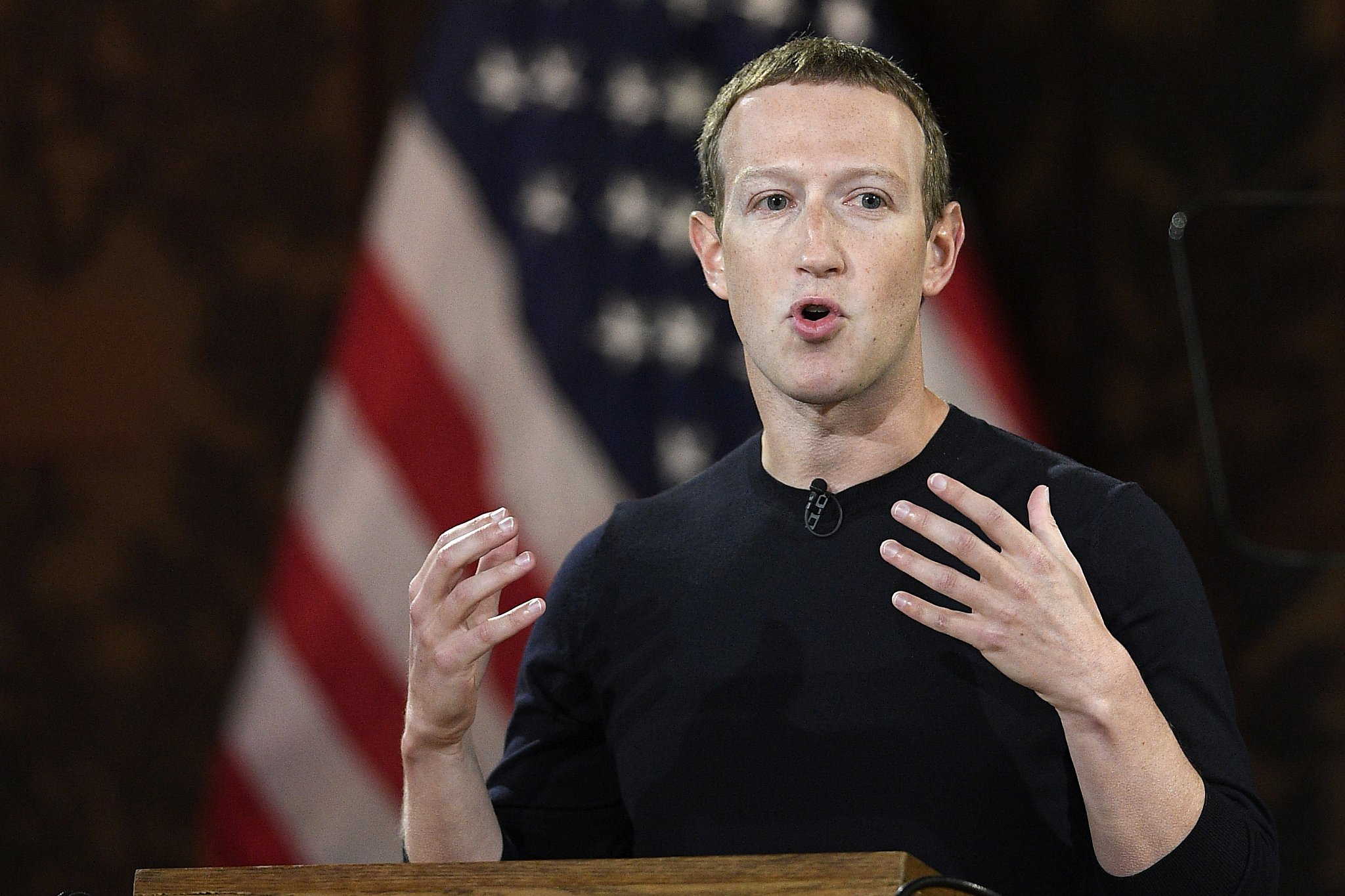
by Kenton Shepard and Nick Gromicko, CMI®
The purpose of the series “Mastering Roof Inspections” is to teach home inspectors, as well as insurance and roofing professionals, how to recognize proper and improper conditions while inspecting steep-slope, residential roofs. This series covers roof framing, roofing materials, the attic, and the conditions that affect the roofing materials and components, including wind and hail.
Rates of Weathering
The speed at which wood shakes and shingles weather depends on a home’s:
- climate zone. Homes located in climate zones that experience severe weather conditions will weather faster than those in zones with mild weather;
- the roof slope orientation. Roof slopes that face south or that face the direction from which storms approach will weather faster than more protected slopes;
- the quality of the shakes or shingles; and
- the quality of the installation. Poorly installed roofs can experience a variety of problems, depending on the nature of the installation:
- They may be slow to dry, which can encourage decay and distortion.
- They may be prone to leakage due to inadequate sidelaps, excessive exposure, or poor fastener placement.
- They may suffer reduced wind resistance due to inadequate fastening or excessive exposure.
Distortion
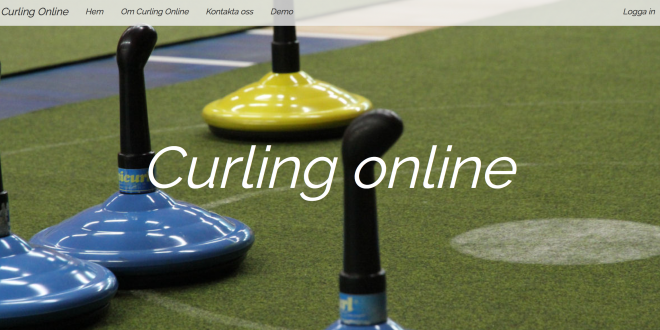
Distortion is a general term that includes cupping, which occurs across the width of the shake or shingle, and curling, which occurs along its length.
Cupping is caused by uneven moisture absorption and drying. As wood absorbs moisture, water fills the spaces between wood cells, causing the wood to swell. As wood dries, water leaves the spaces and the wood shrinks. The undersides of shakes and shingles often dry more slowly than the exposed faces. The exposed faces will shrink as they dry, but the undersides will remain in an expanded condition, since they’re still full of water.
Curling is caused by natural stresses in the wood that are released when the shake or shingle is cut and are made worse by moisture cycling. Flat-grain shakes and shingles are more likely to distort than edge-grain and slash-grain.
Checks
Checks are cracks that don’t extend through the shake or shingle. Cracks that do extend through are called splits. Checks are an aesthetic concern and don’t affect performance.
Splitting
All grades and types of cedar shakes and shingles will crack and split naturally as they weather over time. Flat-grain shakes and shingles are more likely to split than edge-grain, especially along the center of the heartwood, which is why vertical joints should not align with the centerline of heartwood, but should be offset a minimum of 1½ inches.
Splits from weathering are typically wider at the base of the shingle; that is usually where they first develop. Splits that have been open and exposed to weather have rounded edges on the upper surface and are the same color inside the split as on the upper surface.
Newer splits from impact, such as hailstrikes or tree branches, or from footfall or mechanical damage, have sharp edges, and the interior of the split is typically orange. Over several months, the wood will turn grey from exposure to UV radiation and, to a lesser extent, oxidation.
The photo above shows a fresh split from footfall. You can see that it’s orange and runs the length of the shake. The grey color and rounded edges near the butt indicate that the shake was already weakened by a partial split when it was stepped on.
The photo above shows damage from a low-angle hailstrike.
This photo shows a more direct hailstrike.
The photo above shows a shake roof at the end of its useful life. Widespread splitting has reduced sidelaps to less than 1½ inches over a large part of the roof.
Generally, after 10 years’ exposure to weather, one-third of edge-grain and two-thirds of flat-grain shakes and shingles will have splits.
Splits are more difficult to see when wood is wet because, as wood absorbs moisture, it swells, which tends to close splits. For this reason, and because wet wood roofs are slippery and dangerous to walk, they should be inspected when they’re dry.
Causes of Splitting
All shakes and shingles will eventually split. Splitting is part of the natural aging process.
Splits may start at fasteners. If more than two fasteners are installed, shakes and shingles may not be able to swell and shrink freely and may split as a result.
Splits caused by hail have an indentation along the split. If the shake or shingle was cupped at the time of impact, the impact may be to one side of the split, but this condition is relatively rare.
Splits caused by the weight of a person walking have no hail indentation and the split may be roughly uniform in width, as opposed to splits caused by weathering that are wider at the shingle butt, since weathering splits start at the butt.
Results of Splitting
If they extend the length of the shake or shingle and cause it to loosen, the shake or shingle may be more easily blown off or be displaced by someone walking on the roof.
If splits align with vertical joints or other splits in the course below, runoff will have an avenue to penetrate the roof.
If splits are wide enough to expose the felt interlayment to sunlight, UV radiation will deteriorate the felt, eventually allowing moisture to penetrate deeper into the roofing system.
Here, you can see the color difference between new and existing shakes. The new shakes will fade to match the existing shakes (typically, in less than a year), although home site conditions will affect that timeframe somewhat.
**************************************************
Learn how to master a roof inspection from beginning to end by reading the entire InterNACHI series: Mastering Roof Inspections.
Take InterNACHI’s free, online
Play Curling Online
Roofing Inspection CourseMastering Roof Inspections
Roofing Underlayment Types
Inspecting Underlayment on Roofs
Free Curling Games
Fall-Arrest SystemsRoofing (consumer-targeted)